
By
Conor Furstenberg Stott
October
5, 2023
The NH3 Kraken: Amogy’s ammonia-powered tugboat
Building on the success of their previous
technology demonstrations – which featured a 5 kW drone, a 100 kW
tractor, and a 300 kW semi-truck – Amogy is now retrofitting a tugboat
to be the world’s first ammonia powered vessel.
In this episode of Maritime Insights, Abigail Jablansky (Head of
Project Management at Amogy) provided insight into Amogy’s approach to
retrofitting the tugboat (dubbed the NH3 Kraken), and Herbert Fowlkes
(Chief Safety Consultant at Chief Safety Solutions) described how his
organisation is helping to guide Amogy through safety compliance
requirements, and how best to work with regulatory bodies like the
United States Coast Guard. You can download the speaker’s slides here,
and watch a full recording of the conversation here.
Calling in from the shipyard
Calling in from Feeney Shipyard
where the tugboat works are taking place, Abigail took us through the
origin of Amogy, founded three years ago and currently counting USD
220 million in fundraising. Centered in Brooklyn, they also have a
presence in Houston, Norway and Singapore. The tug is 32m in length,
was built in 1957, and currently lies at Feeney (about 2 hours north
of NYC), where she is being converted to feature a new ammonia to
electric powertrain.
Much of the development phase
has been asking: “what does ammonia power mean for such a vessel?” The
initial physical work stages have required a lot of demolition in
preparation for the powerpack and rest of the plant that needs to be
installed. While the original hull form remains the same, much needs
changing in the interior to accept the new equipment. A specific new
space requirement was identified for the ammonia powerpack, including
reworking of reinforcement and renewing of the deck and pilot house.
Most of the existing internal machinery has been ripped out.
In parallel, on the process
design side, Process and Instrumentation Diagram definition continued
while placement of equipment was decided, respecting safety
requirements for ventilation and fire prevention. A continuous HAZOP
evaluation process was required to take such decisions. The first
construction phase in the dry dock was mostly in the interior, where
the engine room was partitioned off forming the powerpack space and a
separate electrical space. Other works included sea chest installation
and necessary frame reinforcing. Where weight assumptions and
estimations had to be made, strength factors of safety were increased.
Hull painting and various pressure testing is now complete, and the
vessel is ready for the next phase: receiving the drivetrain plant.
The plan and
partners involved
.png)
The ammonia tank room is
located furthest forward. It is classified as a hazardous zone and
includes an airlock, and entry is allowed only when authorized. Vector
Systems are supplying the ammonia tank. Immediately aft of this is the
Amogy powerpack room including cooling water pumps, scrubbers etc. Aft
again, we find the electrical drive components and switchboards (SEAM
to supply these).
On the main deck is a forward bunkering station and reconstructed deck
house with control room, where data is to be collected and safe
operation maintained. There are also batteries installed for backup
redundancy and peak shaving. SEAM is the key partner for the power
control distribution. Other technology partners include W-Industries,
Macrotek, Yara & Tanner Industries. Additional project partners
include DNV, Feeney Shipyard, Chief Safety Solutions and the US Coast
Guard. C-Job covered the overall naval architecture requirements.
The Amogy Powerpack: three parts
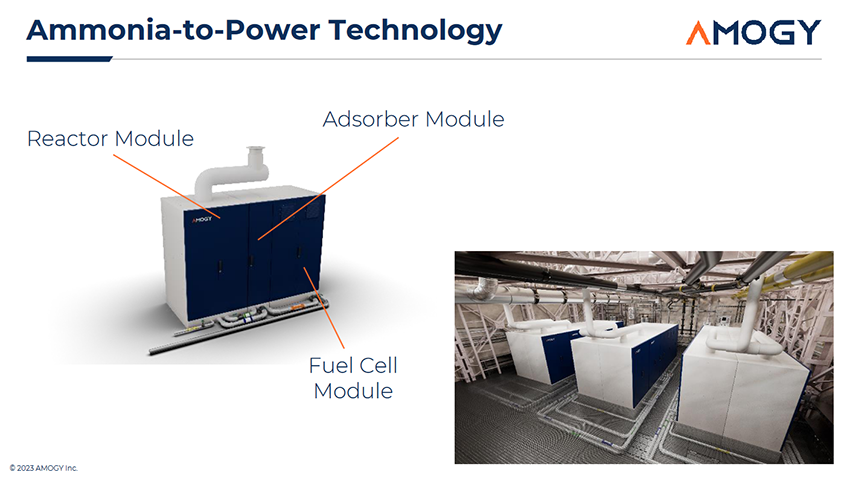
The Amogy powerpack is first
composed of a reactor, which cracks the ammonia to nitrogen and
hydrogen, then an absorber which removes any residual ammonia from the
stream. After this comes the fuel cell module, a low temp PEM which
consumes the hydrogen fuel, converting it to electrical energy &
water.
The modules will be skid installed and connected to the required
piping installation. This method allows for further development &
optimisation, and will provide valuable learnings toward future
maritime applications (many companies are developing similar, fuel
cell-based propulsion systems for maritime vessels). The project is
also extremely valuable for Amogy, being the first on-water
application for its ammonia-to-power technology. When functioning, the
result leverages the best part of hydrogen (its energy potential) but
without the worst part (its storage challenges). This is the central
value proposition of an on-demand ammonia cracking solution.
Including the Coast Guard
Chief Safety Solutions (CSS)
has been critical to unlocking the regulatory aspect of this project
work. CSS partnered with Worley Marine Consulting (WMC) to provide a
direct communication path to the Sector New York Coast Guard, enabling
smooth cooperation with Amogy. The communication journey has thus far
been about review of plans for key work packages like Worst Case
assessment, Safety Equipment, Sea Trials permission, Regulatory Matrix
and construction/installation plan review. WMC, with a strong
background in electrical and plant installation, were able to advise
on best practice from the Coast Guard point of view. Ongoing, CSS &
WMC will assist with onsite construction execution and crew training.
To date, Amogy has been extremely transparent with their project &
proactive in providing information. The willingness to take advice
from CSS, WMC and the New York Coast Guard has not gone unnoticed, and
the open dialogue has allowed significant progress.
How to start such a project?
Starting this project was challenging. The first conversation was with
C-Job, who helped Amogy identify the appropriate vessel type for
conversion. Following this, the huge amount of interest shown by
potential partners across the value chain was key to building
momentum. Everyone involved has been willing to bring in their own
existing insights, but remain flexible to ensure steady progress.
The difference with a “regular” conversion of such a vessel is that
regulations are missing for ammonia. Technology development is moving
faster than regulatory progress, so the methodology is to throw all
possible safety requirements in at first, and scale back later if
appropriate. This process has had the effect of speeding up the
regulatory development mission at the US Coast Guard – a valuable
outcome. In the course of conversation Abigail remarked that “being
the first, we get a lot of possibly excessive safety measures – but
that’s necessary.”
HAZOPs well advanced
There have been two HAZOPs completed with C-Job and DNV. The first
covered vessel design, including specifics around the powerpack and
the new Amogy technology itself. The vessel part drew from vessel
design requirements, existing alternative fuels standards and already
available provisional Class rules for ammonia-powered vessels. The
second HAZOP was a review of the first – meant to both stress test the
original and to bring in any changes or elements which were not
covered in sufficient detail. So, the established circular workflow
process of Design – HAZOP – Closeout – Recycle is well advanced with
the NH3 Kraken project.
What’s next?
Like so many projects of this type, commercialization is the
destination. This is also the final Amogy technology application
demonstration, completing the journey to MW-scale Amogy wants to use
this project to better understand product development in the maritime
industry, making this vessel a kind of “internal customer”. Amogy will
target a few key markets, and scale up is imminent. With 2 – 3 million
tonnes of blue and green ammonia production expected to come online
annually from later this decade, Amogy is positioning itself to have
the technology ready to use this fuel supply. Thus, Norway and
Singapore are strategically active places for them to operate in , and
they are among the first movers.
|