GE installs world's first spiral-welded wind
turbine tower
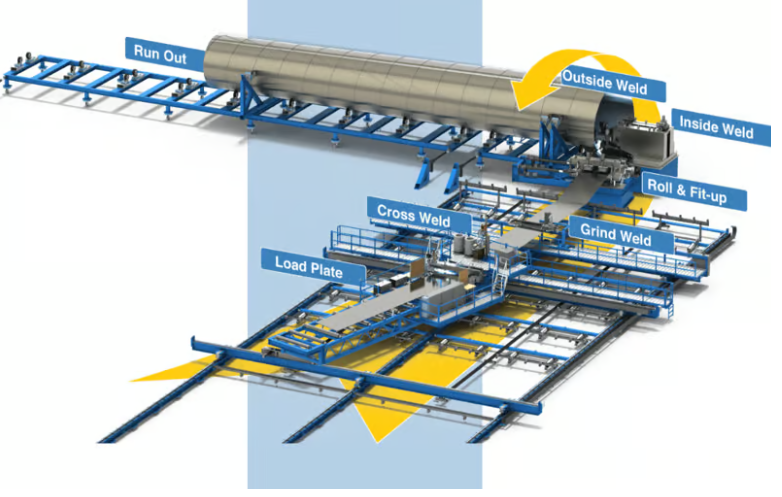
The facilities to manufacture large-diameter pipes on-site at wind
farms can be set up and ready to go within about a month, says
KeystoneKeystone Tower Systems
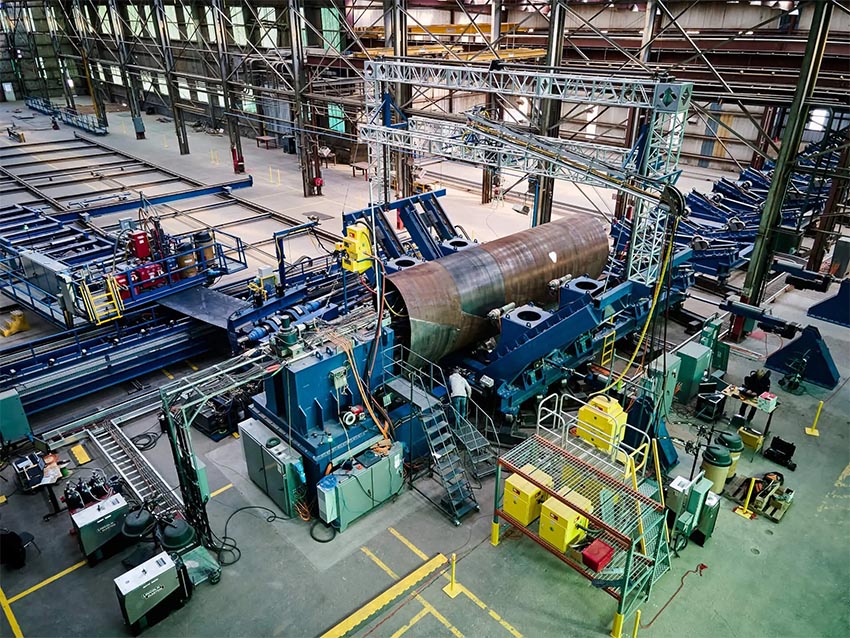
Keystone has set up its own manufacturing facility in Texas, but the
real benefits will start coming when the pipes are rolled
on-site at a wind farm. Keystone Tower
Systems
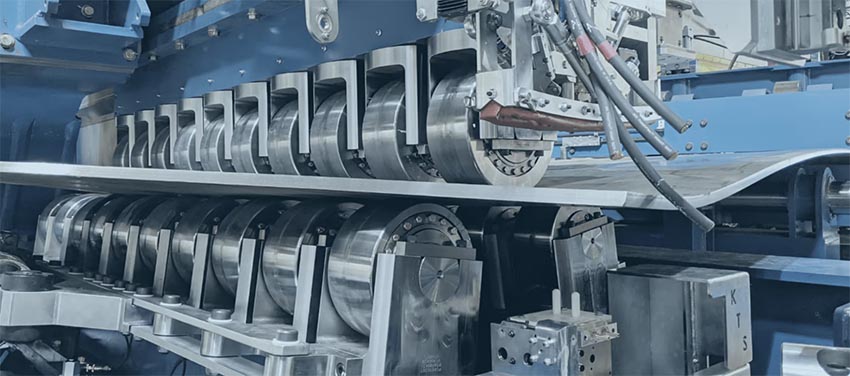
Roller systems bend the sheet or coil steel into shape.
Keystone Tower Systems
Denver's Keystone Tower Systems says it can cut the cost of wind
energy with tech borrowed from pipemaking. It uses spiral welding
techniques to roll sheet steel into huge turbine towers on-site,
stronger, faster and cheaper than current techniques.
The strongest winds tend to be higher up, but as this 2022 study
shows, higher-mounted turbines catching stronger wind doesn't
necessarily equate to the lowest cost of energy. Indeed, once you
factor in the costs of stronger foundations and taller, sturdier
towers, anything above about 120 m (394 ft) tends to result in more
expensive electricity – and in a market as price-sensitive as
energy, that's bad news.
Somewhere around half the Levelized Cost of Energy (LCoE) in an
average commercial wind energy installation comes directly from the
cost of the wind turbines themselves, according to the NREL. Of
that, nearly half of the money's in the nacelle at the top, and the
remainder is split between the rotors, which contribute around 13.7%
to the LCoE, and the tower itself, at around 10.3%.
But as towers get bigger, their share of the upfront CAPEX (capital
expenditure) increases disproportionately. A 110-m (361-ft) tower
might account for 20% of a project's CAPEX, while a 150-m (492-ft)
tower becomes 29% of the cost. And that's not to mention the
additional logistical issues involved in dealing with massive
machinery like this.
Keystone says it's got a tower-making solution that brings the price
of large towers down so low that it "make[s] wind energy the lowest
cost power source available, not just in the open plains, but
throughout the world."
The idea is simple enough; instead of creating a number of
cylindrical "cans," trucking them to the turbine site and welding
them together to create the final tower structure, Keystone proposes
rapidly building small manufacturing facilities on-site, then
trucking in coils of steel in bulk, or even flat sheets, which can
be welded together to form longer strips. These coils or strips are
fed into angled bending machines that bend them into a spiral shape,
which is welded together along the join line continuously as the
steel is turned. Much of the process is automated, as you can see in
the video below.
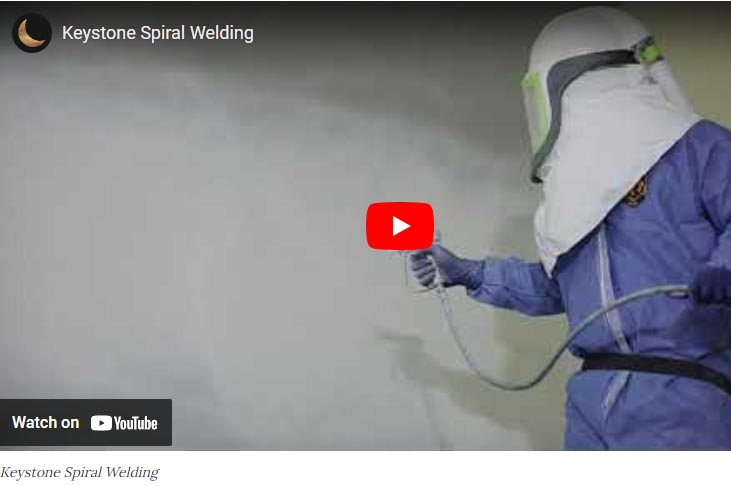
The result, says Keystone, is full-length towers, or shorter
sections if that's logistically easier, churned out 10 times faster
than a standard factory can do them, using up to 80% less manpower.
There may be savings as well in the foundations used for
spiral-welded towers. The factory can be ready to go within about a
month, and building on-site means that you can make the kind of
large-diameter sections that simply couldn't fit under bridges if
you were to make them in a factory and ship them.
This transport restriction, according to Reuters, currently keeps
maximum diameter down to 4.3 m (14 ft) – limiting tower height to
around 80 m (262 ft). Keystone's technology can scale to produce
towers over 7 m (23 ft) in diameter, for towers up to and beyond 180
m (590 ft) high. So onshore wind farms can run taller towers, with
longer blades, driving bigger turbines and producing more energy.
Spiral welding is a well-established technology when it comes to
making pipelines, so the process of creating and quality-inspecting
these long tube sections is already proven. Keystone says it also
results in "better fatigue and buckling performance," enabling
towers of a given height to be made using less steel. And since the
manufacturing plant is essentially mobile, it's easy enough to pop
one temporarily next to a dock and shoot out dozens of sections or
entire towers for offshore installations.
While the mobile factory unit is a key part of Keystone's play, it's
also set up its own manufacturing facility in Texas, and from this
factory it produced the tower for its first live installation,
working with General Electric Renewable Energy.
This first product is an 89-m (292-ft) spiral-welded tower for GE's
2.8-127 turbine. Certified for a 40-year lifetime, the tower is
designed to be a simple replacement for GE's standard towers. It'll
presumably provide a good commercial-scale case study from which to
proceed.
Certainly, Keystone is a small operation at the moment, surviving
largely on US government grants. In this kind of manufacturing, you
need economies of scale to kick in before you can start promising
big savings to customers. But the tower is clearly a significant
part of the cost of a finished wind turbine, as well as a
restricting factor in the size vs power equation, so Keystone's
spiral welding technique could yet become a strong lever with which
to move renewable energy costs.
Source: Keystone Tower Systems via Recharge
Green Play Ammonia™, Yielder® NFuel Energy.
Spokane, Washington. 99212
509 995 1879
Cell, Pacific Time Zone.
General office:
509-254
6854
4501 East Trent
Ave.
Spokane, WA 99212