
By
by Korea
Institute of Science and Technology
October
4, 2023
Study findings may dramatically lower
the cost of producing green hydrogen
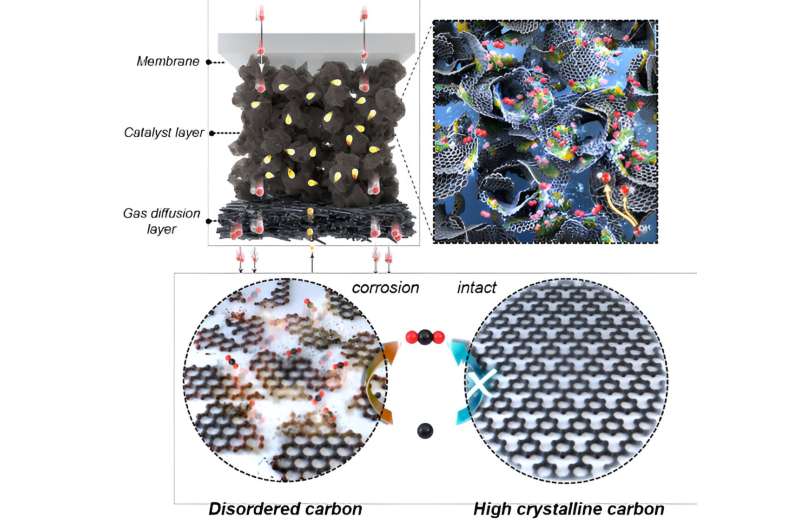
Image of nickel-iron-cobalt layered double hydroxide supported on
hydrophobic crystalline carbon and image of crystalline carbon.
Credit: Korea Institute of Science and Technology (KIST)
According to the International Energy Agency (IEA), global hydrogen
demand is expected to reach 530 million tons in 2050, a nearly
six-fold increase from 2020.
Currently, the primary method of hydrogen production involves the
reaction of natural gas and water
vapor, resulting in what is known as gray hydrogen due to its carbon
dioxide emissions, constituting around 80% of total hydrogen
production. In contrast, green hydrogen is produced through water
electrolysis using electricity, without emitting carbon
dioxide. However, a challenge lies in the inevitable use of
expensive precious metal catalysts, such as iridium oxide.
A research team led by Dr. Yoo Sung Jong of the Hydrogen and Fuel Cell
Research Center at the Korea Institute of Science and Technology
(KIST) have succeeded in significantly reducing the cost of green
hydrogen production by implementing an anion exchange membrane water
electrolysis device with excellent performance and durability by
introducing a carbon support.
Carbon supports have been utilized as supports for various
electrocatalysts due to their high
electrical conductivity and specific surface area, but their usage
has been limited because they readily oxidize to carbon dioxide in
water electrolysis conditions, specifically at high voltages and in
the presence of water.
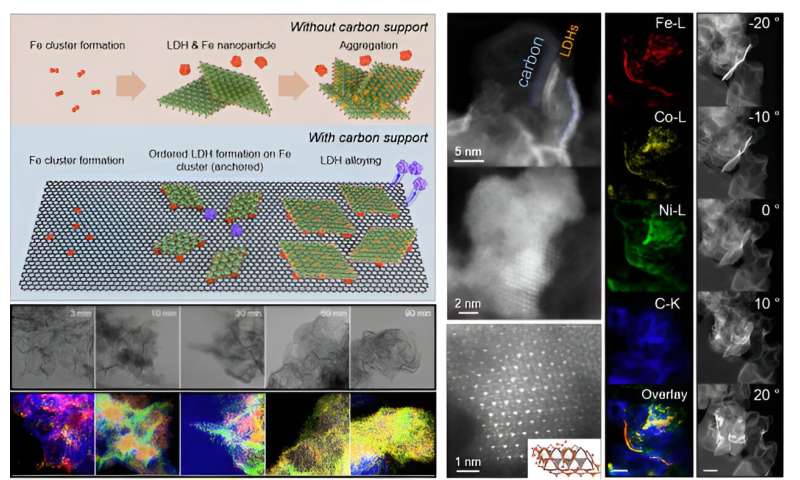
Time-dependent-lapse transmission electron micrograph images of
nickel-iron-cobalt layered double hydroxide synthesis on carbon
support, high resolution scanning TEM and EDS elemental mapping
images. Credit: Korea Institute of Science and Technology (KIST)
.jpg)
The team synthesized a nickel-iron-cobalt layered
double hydroxide material, a significantly cheaper alternative to
iridium, on a hydrophobic carbon support and used it as an
electrocatalyst for the oxygen evolution reaction in anion exchange
membrane electrolysis. The catalyst showed excellent durability due to
the layered structure facing a hydrophobic carbon support and a
nickel-iron-cobalt layered double hydroxide catalyst.
In terms of carbon corrosion, it was found that the generation of
carbon dioxide during the corrosion process was reduced by more than
half, primarily because of decreased interaction with water, a key
factor in carbon corrosion.
As a result of performance evaluation, it was found that the
newly-developed catalyst support achieved a current density of 10.29
A/cm2 in the 2 V region, exceeding the 9.38 A/cm2 current density of
commercial iridium oxide, and demonstrated long-term durability of
about 550 hours. The researchers also confirmed a correlation between
electrolysis performance and the hydrophobicity of carbon, showing for
the first time that the support's hydrophobicity can significantly
affect the water electrolysis device's performance.
"The results of this research confirm the applicability of water
electrolysis devices on carbon supports, which have previously been
limited in use due to corrosion problems, and it is expected that
water electrolysis technology can grow to the next level if the
research focused on catalyst development is expanded to various
supports."
"We will strive to develop various eco-friendly energy technologies,
including green hydrogen production," said Dr. Yoo Sung Jong Yoo in
KIST.
Green Play Ammonia™, Yielder® NFuel Energy.
Spokane, Washington. 99212
509 995 1879 Cell, Pacific Time Zone.
General office: 509-254 6854
4501 East Trent Ave.
Spokane, WA 99212
|