
28
May 2023
By
Will Lockett
Nuclear Steel Could Save 2 Billion Tonnes Of Emissions
Each Year
NuScale & Nucor could
change the world.
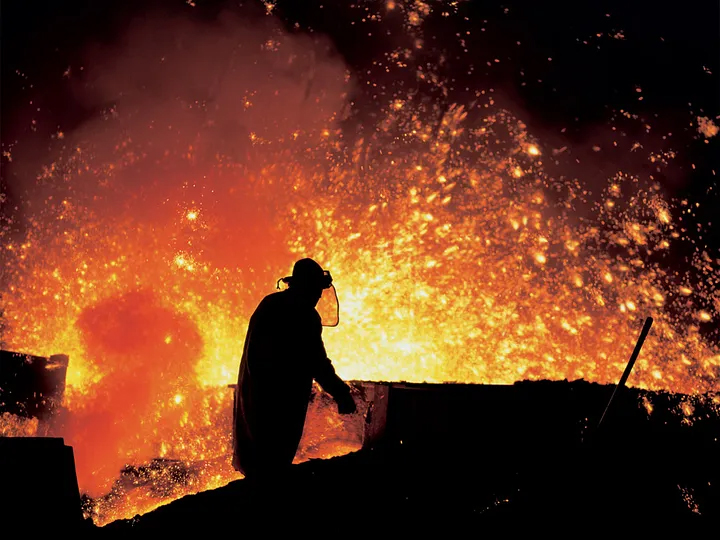
Steel mill — WikiCC
The climate impact of the steel industry is astronomical, producing
over 2.1
billion tonnes of carbon dioxide per year, or 7% of humanity's annual
carbon emissions. These vast pollutants come from the extreme
energy demands of smelting ore and scrap, and as such, the industry is
struggling to find a way to be more planet-friendly. But a US
steelmaker, Nucor, is looking to team up with the Small Modular
Reactor (SMR) nuclear power pioneer NuScale to create ultra-low
emission nuclear steel mills! But how? And can this really help the
steel industry reach net zero?
Smelting is the process of removing the metal you want, in this
case, iron (which will later be turned to steel), from ore or scrap
metal. This involves heating the ore/scrap past iron’s melting point
in a furnace, which is 1800 °C (3270 °F). This molten metal is allowed
to flow out and solidify to form pig iron. Pig iron contains around
20% carbon, making it incredibly low-quality. To turn it into steel,
the pig iron is heated back up to the melting point in an oxygen-rich
environment, and the carbon inside the pig iron reacts with the
oxygen, forming carbon dioxide which is removed, leaving a much purer
form of iron known as steel.
This two-stage furnace process requires a vast amount of energy,
pretty much 24/7, as these plants don’t really close down. This is why
the industry has such a vast carbon footprint. Let me explain.
There are electric-powered furnaces out there, such as arc
furnaces and induction furnaces. So, why can’t they switch to
renewable power? Well, these furnaces require so much power that they
either need on-site
power plants or to be built near power plants, as the grid can’t
handle their energy demands. The problem is that steel mills have a
lifespan on the order of decades, and the vast majority of them
weren’t built with renewables in mind, making
it impractical for them to switch to renewable power, as many
don’t have enough space nearby to install solar or wind power. But, as
the profit margins are incredibly tiny for steelmakers, the cost of
this energy is crucial. Simply, they can’t afford to use cleaner, more
expensive energy, like geothermal or nuclear, which can cost way north
of $100 per MWh. So, they reach for the cheapest practical power
solution, which just so happens to be coal, the dirtiest power out
there.
This is why the vast majority of steelmakers cut out the middleman and
just use coal-fire-powered blast furnaces and don’t muck around with
electricity.
But this is where NuScale comes in, as their VOYGR
SMR technology has the potential to solve the power problems of
the steel industry.
But first, what is an SMR? A small modular reactor is a new design of
nuclear power plant that mitigates some major drawbacks of current
reactor designs.
You see, most modern nuclear power plants consist of several large and
pretty much custom-built reactors that need to be painstakingly built
on-site. This dramatically
increases the cost of building a nuclear power plant, which in
turn drives up the price of nuclear energy, and means it
can take well over a decade to build one.
SMRs, by contrast, use tens of small modular reactors working together
to make a power plant. These reactors are so small they can be built
in a single off-site factory at scale and then shipped to the power
plant site to be installed. This dramatically reduces the complexity
of manufacturing and setting up the reactors and enables the economies
of scale to kick in (as one reactor factory can build enough reactors
for hundreds of sites). As such, SMRs promise to be far cheaper and
far quicker to build. They are also far more flexible, as you only
need to order the number of reactors that you need.
This is why it is fascinating that NuScale
has signed a memorandum of understanding with North American steel
manufacturer Nucor to explore the deployment of NuScale’s VOYGR SMR
power plants at Nucor’s scrap Electric Arc Furnace steel mills.
This means that the companies will assess site suitability and
economies of using NuScale plants to be sited near and provide
ultra-low carbon electricity (as nuclear is the lowest carbon form of
energy we have) to Nucor steel mills.
You see, right now, there are no SMRs on the market, and NuScale’s
VOYGR SMRs are set to be the first to get regulated for use in the US.
What’s more, they have
a project cost per MWh of $89, putting them on par with US
coal energy which costs $88 per MWh.
Nucor’s scrap Electric
Arc Furnace steel mills are only single-stage, meaning they don’t
produce pig iron from ore and instead smelt scrap metal to form a
higher quality metal. This means they use less energy per kg of steel
produced, and so even if NuScale’s predicted cost per MWh rises (which
has already happened), they can stomach it. What’s more, they only
need a handful of NuScale’s VOYGR SMRs to power their mills, meaning
that building these nearby power plants should be cost-effective and
only take a few years to complete. The VOYGR SMRs are also incredibly
compact, meaning it should be straightforward for Nucor to find the
space to install them near their mills.
So if a deal with Nucor and NuScale goes ahead, how big of an impact
will it have? Well, Nucor only produces around 20 million tonnes of
carbon dioxide per year, so in terms of emissions, they are a tiny
player in the steel world. So, even if Nucor fully adopted NuScale as
a power source, it will have and minuscule overall impact.
But, if NuScale and Nucor can prove that SMR technology and steel
mills can work hand in hand, they have the potential to demonstrate to
the world how to decarbonise one of the planet’s most polluting
industries. There are other issues to sort out here, like ensuring
safety, increasing nuclear fuel production and managing the extra
nuclear waste that will come from these reactors. However, all of
these have already proven practical solutions. So don’t be surprised
if, in a decade or so, the steel industry has gone nuclear.
Green Play Ammonia™, Yielder® NFuel Energy.
Spokane, Washington. 99212
509 995 1879 Cell,
Pacific Time Zone.
General office: 509-254
6854
4501 East Trent Ave.
Spokane, WA 99212
|