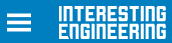
Advancements in green hydrogen production with rare
metals
Boosting green hydrogen: Korean researchers reduce rare metals in
production
By
Daniel Lehewych
June 2, 2023

Green hydrogen, a key player in efforts towards a decarbonized
economy, has been facing a major hurdle due to high production costs.
As reported in Newswise,
the costs primarily come from the need for expensive rare metals, such
as iridium and platinum, used in polymer electrolyte membrane water
electrolysis devices that produce this eco-friendly hydrogen.
Yet, breakthrough technology from the Hydrogen and Fuel Cell Research
Center at the Korea Institute of Science and Technology (KIST) could
be a game-changer.
Green Hydrogen Breakthrough
Led by Dr. Hyun S. Park and Sung Jong Yoo, the research team has
developed a way to significantly decrease the amount of platinum and
iridium required in the protective layers of these electrolysis
devices. Even better, this reduction doesn't compromise performance or
durability – two crucial aspects of large-scale usage.
Here's the twist. Instead of focusing solely on reducing the quantity
of iridium catalyst, as previous studies have done, these researchers
have replaced the precious metal in the protective layer with
inexpensive iron nitride, which possesses a large surface area. Then,
a smaller quantity of iridium catalyst is uniformly coated over it.
The result? A marked increase in the economic efficiency of the
device.
Green Play Ammonia™, Yielder® NFuel Energy.
Spokane, Washington. 99212
www.exactrix.com
509 995 1879 cell, Pacific.
exactrix@exactrix.com
|